The Value-Added Processing & Co-Manufacturing brief examines food processing plants, shared-use and collaborative commercial kitchen resources, or licensed homestead food operations that process local fruit, vegetables, and meat into value-added or lightly processed food products and prepared foods. This Issue brief is one of 27 briefs created as part of the NH Food and Agriculture Strategic Plan.

What's at Stake?
Value-added processing allows New Hampshire farmers and fishermen to expand the volume and variety of their product offerings and more easily compete with larger, out-of-state operations. Value-added processing can provide small-scale New Hampshire farms and fishermen access to new, stable, and predictable markets, create value in bumper crops that would otherwise go unsold, and extend sales outside the primary growing season, all activities supporting long term profitability and viability. The current regulation ecosystem for value-added producers, entrepreneurs, and food manufacturers in New Hampshire is burdensome, inefficient, and difficult to navigate and creates significant challenges for farmers, fishermen, and entrepreneurs

Current Conditions
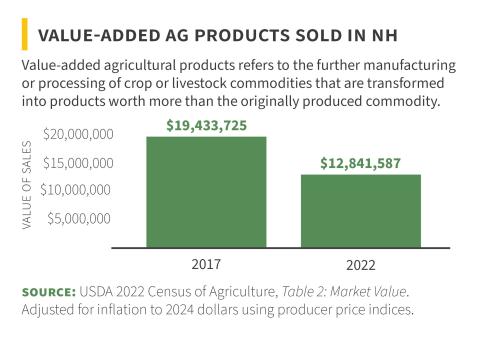
There is a complex regulatory landscape around value-added food production. With two state agencies overseeing inspection, licensing, and regulations, there are many avoidable inefficiencies and confusion that could be streamlined by housing all responsibilities under one agency. In addition to inefficiencies, limited state capacity to provide process reviews for value-added products is another source of strain on New Hampshire’s small food businesses.
In order for a New Hampshire value-added producer to manufacture acidified or predominantly acid foods, their products must comply with the Code of Federal Regulations (CFR) Title 21 part 114, which requires a process review of all products. Once the process review is complete, then the Food Protection Bureau at the NH Department of Health and Human Services will issue a manufacturing license to the producer. To obtain a process review, a designated food safety expert must assess the recipe and production procedures for each product. Currently, there are no process authorities in New Hampshire, which forces New Hampshire’s value-added producers to outsource their process review needs to the University of Maine or Cornell University (the nearest process authorities) where businesses are charged nearly double due to being an out-of-state business.
Value-added producers need more support to access infrastructure and resources. There are no USDA-certified shared-use facilities for processing meat into prepared foods (i.e., soups, pot pies, meatballs) in New Hampshire. Resources are needed to help farmers assess the financial opportunity of value-added production and to help entrepreneurs prioritize the use of local foods.

Challenges
> Value-added producers lack market and distribution access to statewide and regional market channels.
> The confusing and inefficient nature of regulations pose serious barriers to businesses wanting to incubate or enter value-added production.
> There are product pricing challenges; in addition to ingredients and packaging, businesses must cover the costs of labor, processing, transport, licensing and inspections, specialized equipment, food safety management, recipe development, storage and distribution, and be at a large enough scale to meet supply and demand to maintain profitability.
> The USDA regulations to license and operate a certified commercial kitchen to process meat are difficult to justify financially and implement for the majority of New Hampshire’s farms and shared-use commercial kitchens. Food manufacturers are disincentivized to source locally due to the additional logistics of working with local growers.
Opportunities
> The NH Food Hub Network and the New England Food Hub and Processors Network are actively working to address distribution and market channel improvement in the state.
> The Legal Food Hub has existing programs to support food businesses navigating the regulatory environment.
> UNH Extension, the Regional Economic Development Center (REDC), and the NH Small Business Development Center (NH SBDC) provide valuable business planning assistance to farmers, including financial analysis of new enterprises.

Recommendations

Organizations working on this issue
is an organization or program missing from this list? Let us know.

Authors
Lead Author
Rose Wilson, Owner, Rose Wilson Consulting LLC
Contributing Authors
Mary Macdonald, Co-Founder and CEO, Genuine Local
Stephanie Zydenbos, Founder and CEO, Micro Mama’s
Neelima Gogumalla, Founder and CEO, Creative Chef Kitchens
This brief was developed through a participatory process led by the NH Food Alliance, a program of the University of New Hampshire. The brief content is comprised of the opinions, perspectives, and information gathered by the authors and participants, and does not necessarily represent those of the NH Department of Agriculture, Markets, and Food or the NH Food Alliance.
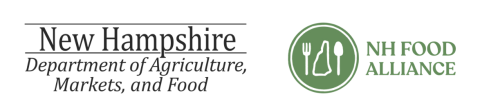
Head to the NH Food and Agriculture Strategic Plan main page to read more briefs, browse recommendations and learn how the strategic plan was created.